In the realm of mechanical engineering, few components are as pivotal to system functionality as the gearbox. Among the various types of gearboxes in use today, the universal gearbox stands out for its versatility and widespread application. However, a critical question arises: how efficient is the universal gearbox in terms of power transmission? This article seeks to explore this question, shedding light on the mechanics, advantages, and limitations of universal gearboxes, while also evaluating their overall performance in real-world applications.
Understanding the Universal Gearbox
At its core, a universal gearbox is designed to transmit power across a range of rotational axes. Unlike traditional gearboxes, which operate on fixed or linear axes, universal gearboxes are adept at transferring motion and torque between shafts that may not be aligned in a straight line. This ability to adapt to a range of angles makes the universal gearbox invaluable in complex systems such as automotive drivetrains, industrial machinery, and robotics.
The central component of the universal gearbox is the universal joint, often referred to as a U-joint. This joint is responsible for facilitating the transmission of rotational power between shafts that are not in direct alignment, making it an essential part of many dynamic systems.
The Mechanics of Power Transmission
The efficiency of any gearbox, universal or otherwise, hinges on its ability to transmit power with minimal loss. Power transmission efficiency is generally defined as the ratio of power delivered by the output shaft to the power supplied to the input shaft. Ideally, an efficient gearbox should minimize friction, slippage, and energy dissipation during the transfer of motion.
In a universal gearbox, however, several factors can influence this efficiency. The inherent angular misalignment of the shafts, for example, can lead to changes in the velocity ratio between input and output. As the U-joint rotates, the velocity of the output shaft may fluctuate, a phenomenon known as the "variable velocity" effect. These fluctuations can introduce additional energy losses, which impact the overall efficiency of the gearbox.
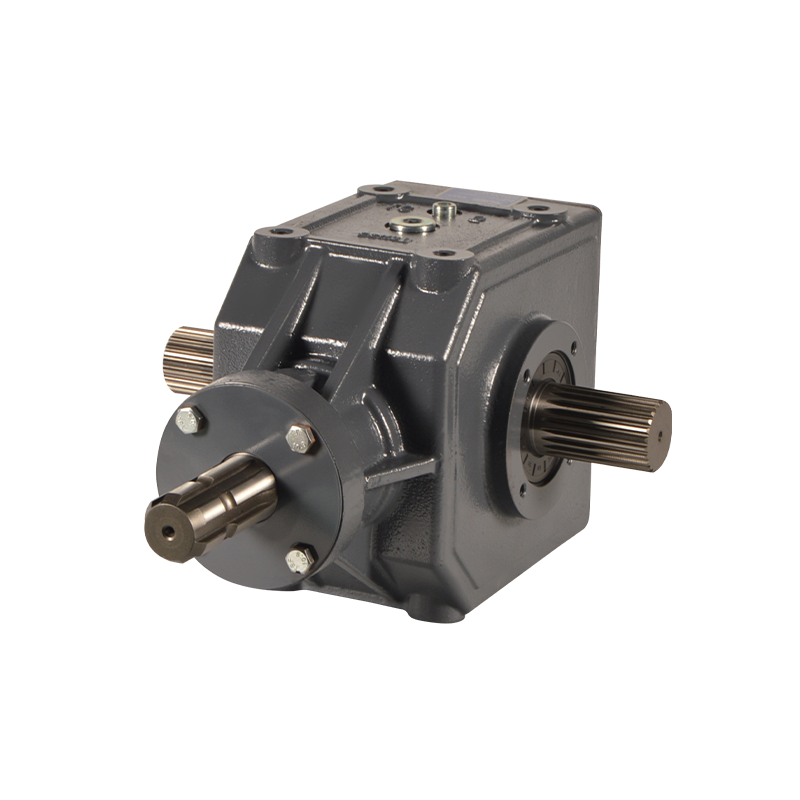
Furthermore, the complexity of the U-joint mechanism itself—while enabling angular movement—can also create frictional forces that result in energy losses. The quality of materials, the precision of manufacturing, and the type of lubrication used all play significant roles in mitigating these inefficiencies. High-grade materials and advanced lubrication systems can reduce friction and, in turn, improve the power transmission efficiency.
Advantages of Universal Gearboxes
Despite their potential efficiency challenges, universal gearboxes offer a number of compelling advantages. Their ability to transmit power across non-parallel shafts makes them indispensable in scenarios where space constraints or complex mechanical layouts require flexible solutions. In the automotive sector, for instance, universal gearboxes are integral to the drivetrain systems of vehicles, where they allow the transmission of power from the engine to the wheels, even when the driveshafts are not in a direct alignment.
Moreover, universal gearboxes excel in applications where torque needs to be distributed across different angles or in multi-axis systems. In these settings, the ability of the gearbox to maintain functionality despite angular displacement is a key benefit. This versatility makes universal gearboxes a preferred choice in industries ranging from aerospace to robotics.
Efficiency Challenges and Limitations
Despite their advantages, universal gearboxes are not without their limitations. The variable velocity effect, which leads to inconsistent rotational speeds, remains a significant challenge, particularly in high-speed applications. In such cases, the resulting energy loss can be substantial, reducing the overall efficiency of the system. In addition, the presence of multiple moving parts in a universal gearbox can lead to wear and tear over time, further diminishing efficiency.
Another issue is the sensitivity of the universal joint to misalignment. While the design of universal gearboxes allows for angular flexibility, excessive misalignment can cause undue strain on the system, increasing friction and leading to premature failure. Ensuring that the gearbox is properly calibrated and maintained is essential for minimizing these risks and preserving efficiency.
Balancing Efficiency and Versatility
The efficiency of the universal gearbox in power transmission is influenced by several factors, including the design of the universal joint, the precision of the components, and the quality of the materials used. While the gearbox may not always achieve the same levels of efficiency as other types of gearboxes, its unparalleled versatility makes it indispensable in many complex systems. By understanding its limitations and ensuring proper maintenance, engineers can optimize the performance of universal gearboxes, striking a balance between efficiency and functionality.
In the end, the universal gearbox remains a cornerstone of modern mechanical design—enabling power transmission across a wide array of applications, despite its inherent efficiency challenges.